HVAF or High Velocity Air-Fuel is a thermal spray process for deposition of coatings for protection of parts, vessels and structures against abrasion, erosion and corrosion.
Common uses:
- abrasion protection
- erosion protection
- corrosion protection
- surface restoration
- diameter build-up
- spraying of internal diameters of pipes
- thin layer surface alteration to prepare for other processes such as galvanization
- surface preparation by cold or hot grit blasting
- coating stripping by hot grit blasting
HVAF coatings are similar to and generally comparable to coatings produced by HVOF and Cold Spray. HVAF is a "warm spray" process that is cooler than HVOF, but hotter than Cold Spray. HVAF guns utilize axial powder injection into an air-fuel jet with a temperature of about 1900-1950°C. Therefore, the process is capable of effectively applying carbide-based materials, but since the air-fuel jet produces considerably less oxides than high temperature oxy-fuel jets, the HVAF process can also apply metals with almost zero oxidation, similar to Cold Spray. All common thermal spray powder materials may be applied with HVAF, except for ceramics.
The HVAF process runs on a fuel gas such as Propane, Propylene, or Natural gas (supplied from cylinders or gas line at 140 psi), and compressed air (supplied by a 400 CFM air compressor at 125 psi). There are no additional requirements for cooling or operation.
Operating Requirements for the M3™ HVAF spray system:
Compressed Air: 125 psi, 250-260 CFM (400 CFM air compressor required for start-up)
Fuel Gas: 140 psi
HVAF can apply metal, carbide, and metal alloy powders of 5 to 53 micron range, with -30+10 µm cut being the most common. The deposit efficiency (D.E.) is 50-75% for carbide powders, and 60-85% for metal powders.
HVAF process is capable of spray rates of up to 30 kg/h of carbides, and up to 23 kg/h of metal powders (M3™ spray system).
The theoretical limit of the HVAF jet velocity is 1400 m/s for pressure ranges that could be provided by regular 125 psi air compressors. The particle velocity is up to 1100-1200 m/s and depends on the powder cut and spray gun size and design (accelerating distance and nozzle profile).
Tungsten carbide is the predominant material applied by HVAF for abrasion wear resistance. With -30+10 µm powder cut, coating hardness of up to 1700 HV300 can be achieved with D.E. of 50-55%.
Tungsten carbide (86WC-10Co-4Cr) HVAF coatings demonstrated 90-185% higher wear resistance when compared to Super D-Gun in ASTM G65.
HVAF coatings generally have very high bond strength. For HVAF-sprayed WC-based coatings, with or without grit blasting, the typical bond strength exceeds 12,000 PSI, which is the limit of regular glue adhesion bond strength testing equipment. HVAF coating bond strength is not conventionally measurable due to preliminary glue failure in normal testing equipment. Alternative braze adhesion bond strength testing was developed, which determined the bond strength of HVAF-sprayed Inconel 718 to be 29,000 PSI (200Mpa).
One notable characteristic of HVAF coatings is the substantial resistance to stress-induced delamination. Coatings are non-brittle and are capable of withstanding significant mechanical deformation, as high bond strength to substrate prevents peel off. In testing substrates with tungsten carbide coatings were bent at 90° over 0.5" diameter, yielding no coating delamination. In alternative tests, coated samples were stretched to failure, producing no coating separation.
As with fatigue and stress testing, HVAF coatings exhibit very good impact resistance. In an impact test a 1 lb steel ball was dropped from a height of 5 feet. Typically HVOF and supersonic plasma can withstand 18-22 hits before failure, as shown in plasma WC/20Cr3C2/7Ni coating on the left. On the right is an HVAF WC/20Cr3C2/7Ni coating sprayed with M3™ spray gun that withstood 100 hits and the test was stopped.
WC/20Cr3C2/7Ni - Plasma Sprayed 18-22 hits to failure ![]() |
WC/20Cr3C2/7Ni - HVAF (M3™) Sprayed 100 hits, test stopped ![]() |
Tungsten carbide based and chrome carbide based HVAF coatings sprayed with M3™ HVAF system were determined to be impermeable in 15,000 PSI gas-permeability testing, as sprayed. No sealant application was required, which is a necessary step for similar HVOF coatings.
The porosity of M3™ sprayed HVAF coatings is not detectable or below 0.5% with most materials.
WC-10Co-4Cr (-30+5) µm ![]() |
Copper (-45+15) µm ![]() |
WC/20Cr3C2/7Ni (-25+5) µm

Carbide HVAF coatings can be routinely deposited to 1000 µm thickness, with up to 40-50 µm applied per pass. In testing up to 12,000 µm coatings were achieved with tungsten carbide. Metals can routinely be applied to 8000 µm thickness or more, with 100 µm applied per pass.
The photograph below shows a 8mm thick tungsten carbide coating.
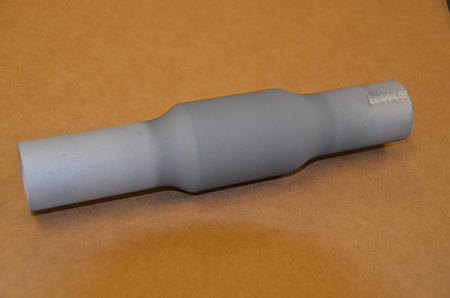
WC-12Co coatings sprayed with M3™ spray system can withstand 3.5GPa contact pressure, which is 75% higher compared to what the other best coatings could provide in comparative testing. Modern CVTs (Continuously Variable Transmissions) were developed with HVAF coatings.
HVAF coatings can be corrosion resistant "as sprayed" with no additional sealant application.
The HVAF process generally forms coatings from softened (but not molten) particles, which produce a peening effect that builds up compressive stresses in the coating. Shown below is an electron microscope micrograph of HVAF-applied copper powder particles (-45/+10 micron cut) impinged on an aluminum alloy substrate.
HVAF coatings exhibit an extremely low level of oxidation, similar to Cold Spray.
Low temperature of the HVAF process prevents overheating of the powder material, in contrast with the hot jets of conventional thermal spray processes (such as plasma, HVOF, or detonation spraying). As a result, the particles are mostly solid upon impact on a substrate, which slows down diffusion of oxygen by several orders of magnitude compared to liquid metal.
![]() | Material: Ni-45Cr-1Ti |
The micrograph below shows an HVAF (M3™ sprayed) copper coating on aluminum substrate. Thickness of the Coating: Approximately 1,200 microns (120 microns per pass)
- Same degree of oxidation as cold spray coatings
- Near 0% porosity
- Spray rates up to 50 lbs/hr
- Deposit efficiency 85%
- No grit blasting needed
- Low cost of application
The Surface Side of the Coating, x300: | The Substrate Side of the Coating, x300: |
Spraying of carbide powders with HVAF does not produce any nozzle build up. The tendency for nozzle build up with metal powders is low to moderate, and can generally be reduced or eliminated completely by powder cut selection and adjustment of operating parameters and nozzle configuration.
HVAF spray gun design permits dual-purpose use for surface preparation before spraying. The robotic manipulator can execute the same sequence that is used for spraying while grit is supplied to the spray gun, providing conventional grit blasting capability. "Hot" grit blasting is done by supplying grit to the gun while the gun is running, producing very high grit velocity. Hot grit blasting can be used for rapid surface preparation, up to 50 times faster than conventional grit blasting, but may also be used to strip existing coatings off parts before spraying.
The photograph below shows "hot" grit blasting performed on the internal diameter of a part.
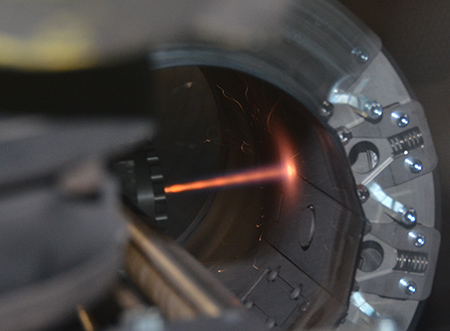
The HVAF process is substantially less expensive in setup and operation than HVOF, Plasma, or Cold Spray, but more expensive than Arc Spray metalization. As HVAF coating quality is comparable to HVOF and Cold Spray, refer to their respective pages for detailed economic comparison.
HVAF spray guns as small as 55 mm can apply coatings to internal diameters of pipes and parts as narrow as 80 mm. With no inherent restriction on length, pipes as long as 40 ft and more can be internally coated.
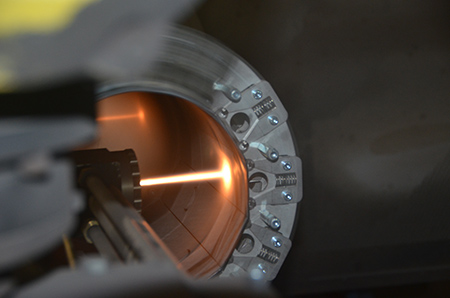
- JP-5000™ is a trademark of Praxair S.T. Technology, Inc.
- Diamond Jet™ is a trademark of Sulzer Metco Management AG
- M3™ is a trademark of Uniquecoat Technologies, LLC